PUMEX® Casing System
At Drillco®, our PUMEX® system bits are designed to optimize performance in challenging mining environments. These bits are most effective when used with our DTH Hammer PM5.2 or within the 5-inch hammer range, ensuring efficient overburden drilling and precise casing advancement. Ideal for drilling through complex geological layers, these tools provide superior durability and precision, minimizing downtime and maximizing productivity. Trust Drillco® for cutting-edge drilling solutions that enhance your mining operations with the latest advancements in technology.
PUMEX®
Revolutionizing drilling with simultaneous casing and protection.
Drilling in grounds like gravel, boulders, sands or any kind of loose or fractured overburden, becomes almost impossible under the conventional drilling methods due to the collapse of the hole and the following fill of material inside the hole.
System bits
Innovating safety with simultaneous drilling and casing.
The PUMEX® system permits doing, at the same time, the drilling of the hole and its casing, leaving an inner protection that avoids the falling down of material inside the hole and eliminates the risk of loosing drilling tools.
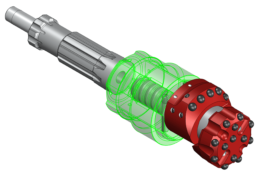
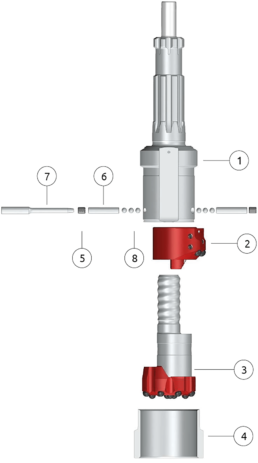
complex SYSTEM
Our PUMEX® system bits
With a strong focus on safety, the PUMEX® system mitigates hazards associated with loose materials, making it a reliable choice for any mining operation.
SYSTEM COMPONENTS
1.- GUIDE DEVICE
2.- REAMER
3.- PILOT BIT
4.- CASING SHOE
5.- ELASTIC BOLT (CONNEX)
6.- LOCKING PIN
7.- PUNCH (Element for the assembly)
8.- LOCKING BALLS
PRINCIPLES
PUMEX® system functioning is based in the hole’s reaming and drilling.
PUMEX® system functioning is based in the hole’s reaming and drilling. The Pilot Bit rotating axle is displaced with respect to the drilling string axle. When the system rotates to the right, the Reamer opens describing an angle slightly bigger than the casing pipe (see Fig.1). When the system rotates to the left, the Reamer closes to a diameter smaller than the guide, permitting this way, the system to be taken out of the hole, passing through the inside diameter of the Casing Shoe and the casing a pipe (see Fig. 2).
The driving of the casing happens through the transmission of the hammer impact energy from the Guide Device to the Casing Shoe.
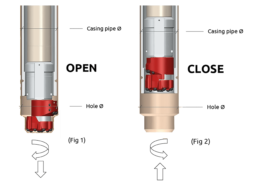
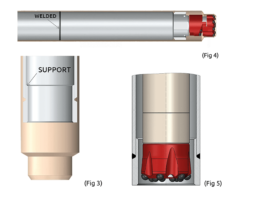
The support between Casing Shoe and Guide Device is done over an annular ring in the Casing Shoe. It is not necessary to rotate the casing pipes, since they are always free while drilling (see Fig 3). The Casing Shoe is attached to the pilot pipe (which differs from the rest of the casing pipes by being shorter) by a welding string. The following pipes are being added as the drilling goes deeper, their union can be welded or threaded (see fig 4). After reaching the desired depth, drilling can continue with a conventional system, taking care that the bit’s O.D. is smaller than the Casing’s I.D. (see fig 5).
If the casing pipe is to be recovered, once the drilling is over, it is recommended the pipe union to be threaded.